ぶちゅまるです。
作業現場において、フォークリフトの運転は欠かせない存在です。
しかし、運転中の危険行為による労災事故の発生は深刻な課題です。
「荷物をひっくり返したり、シャッターに衝突したり、荷棚を破壊してませんか?」
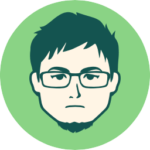
ええ、そうです。僕の実体験です。笑
ぶつかったのが人じゃなくて本当に良かったです。
勿論、上司にこっぴどく怒られたんですけどね……。
本当にフォークリフト運転中の安全意識は大切です。
この記事では、
フォークリフトの運転中の安全5原則について詳しく解説します。
最近、安全講習を受けて気が引き締まったので、皆さんに内容を紹介したいと思います。
労災事故が起きる要因として物・人・管理に着目する必要があります。
労災は「不安全な状態と行動が重なった時」に起きると言われています。
では、具体的にはどのように労災事故は起きるのでしょうか。
フォークリフト安全5原則って何?
以上のような法則をフォークリフト安全5原則と言います。
労災事故の要因解析をして経験的に導かれた内容です。
それでは、フォークリフト安全5原則を怠った場合、
どのような危険行為をしてしまうのでしょうか。
危険行為は労災事故に繋がる可能性が高いので
以下で例を見てみましょう。
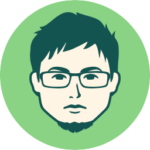
知らないうちにやってしまっているかも……。
フォークリフト運転中の危険行為と労災事故の発生要因
http://www.jiva.or.jp/pdf/22_SafetyDay_1-1.pdf
厚生労働省によるフォークリフトに起因する災害発生件数の推移です。
データを見ると分かるように毎年、数千件以上の労災事故が起きています。
死亡事故は減少傾向ですが、まだまだ労災事故は多いです。
フォークリフト運転中の危険行為や労災事故の発生要因について解説します。
危険行為の実態について理解することで、労災事故を防ぐ為のルール作りや対策方法について知ることができます。
危険行為について
フォークリフトの安全5原則を正しく理解した上で、
フォークリフトの基本ルールを知っていれば、危険な運転をすることはないでしょう。
しかし、いつかはヒューマンエラーが起きてしまいます。
実際に「どのような危険行為で事故が起きてしまうのか」について紹介します。
誤操作による暴走
- 走行運転の操作
- フォークの操作
- 爪幅の調整
具体的に言うと、運搬中や走行の際の注意不足などが考えられます。
スピードを出しすぎていたり、急な旋回を行なっているなどが例です。
また、フォークの操作を誤って荷物を転倒させたりなども考えられます。
この際に人を巻き込めば、労災事故に繋がるかもしれません。
運転をする際は、危険予知が重要です。
走行時の安全確認や法律の違反を行う
周りを確認せずに、旋回や走行を行うと危険です。
フォークリフトは爪がある分、旋回する際の幅が広く、
特に後方の確認を怠ると、他の作業者を轢いてしまう可能性があります。
作業範囲内に人を入れないことが大切です。
また、無資格で運転する等の法律違反を行わないようにしましょう。
責任を負うのは運転者本人になります。
黙認している場合、会社にも罰則があるので注意しましょう。
フォークリフトの点検や整備不足
フォークリフトの点検や整備は定期的に行い、管理しましょう。
日常点検や定期点検をしなければ、異常を発見できません。
異常を整備しない状態で作業をしていると、
正しい運転操作を行なっていても、
整備不足で事故が発生する可能性があります。
重大な事故に繋がらないように、点検と整備はしっかりしておきましょう。
パレットや荷物の養生不足
- パレットの破損
- 荷物の養生不足
- 荷物の偏り
- パレットと荷物の摩擦の少なさ
荷物を運搬する際に使うパレットですが、木製やプラスチック製があります。
これらが破損している場合や荷物を乗せた際の相性によっては摩擦が少ない為、
正しい作業手順で運搬を行なっていても荷物の落下などに繋がり、
重大な事故につながる可能性があります。
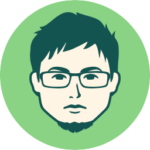
特にパレットと荷物の容器がプラスチック同士だった時は、
滑りやすくてヒヤッとしたなぁ。
加えて、偏った重心では不安定で積荷が安定しないので重心を考えて積荷を置き直しましょう。
パレット等を運ぶ際もはみ出して重ねないようにしましょう。
どうしても偏りが起きてしまう場合は、
ストレッチフィルム等でしっかりと養生することで転落や転倒のリスクをなくす事ができます。
運転者が安心して作業できるように可能であれば養生を見直すのも一つです。
作業エリアの共有
人が行き来するような場所でフォークリフトを操作してはいけません。
基本的には、運転者が周りの確認を行ってから作業すれば事故は起きません。
しかし、物陰から作業者が出てくる場合もあると思います。
また、荷物の後ろに隠れて死角になっていたりする場合、
運転手が見落とす可能性もあります。
他の作業者が徘徊していると、荷物に集中している運転手はあまりにも多くのことに気を遣わなければなりません。
その為、作業エリアを分けて職場の作業者と運転手にとって、より安全で効率の良い現場を作る必要があります。
作業場の共有をする場合は、誘導員を配置して作業しましょう。
慢心運転
慣れてくるとフォークリフトを手足のように簡単に扱えるようになります。
作業スピードが上がっていくので速度も出ますし、基本的な確認を怠ってしまいます。
作業速度が上がると、確認する時間も短くなります。
特にフォークリフトの爪の入り具合や周囲や後方への確認を怠ると、
重大な労災事故につながる可能性があるので注意しましょう。
労災事故の事例と発生要因
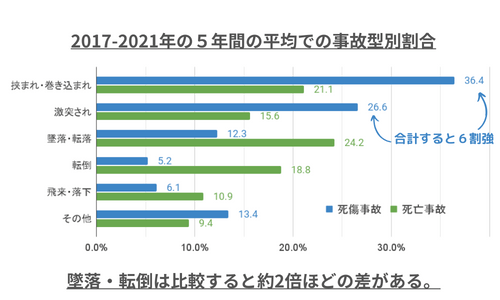
悲しい話ですが、フォークリフトでの事故は重大なものになる事が多いです。
特に「挟まれ・巻き込まれ、激突され」は合わせると死傷事故の割合が6割強となっており、死傷事故の大半を占めています。
また、墜落・転倒では死亡事故の割合が高く、非常に危険であることが分かります。
以下、実際にあった労災の事例を要約して発生要因を解説します。
挟まれ・巻き込まれ
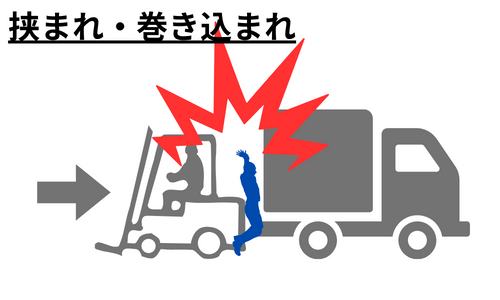
雨天時、屋内作業場で被災者がトラックへ荷積みを行うため、荷台の扉を開けていた。近くでフォークリフトによる荷物移動を行っていた作業者は、被災者のトラックを視認したものの、人の姿は見えなかったためフォークリフトを後退させた。トラックの荷台の側にいた被災者はフォークリフトとトラックの間に挟まれて死亡した。フォークリフトの誘導員は配置されていなかった。
- 誘導員を配置することなく、労働者をフォークリフト付近に立ち入らせたこと。
- フォークリフトおよびトラックについて、運行経路を含む作業計画を定めていなかったこと。
- 同一の場所で荷積作業を行っていた作業者間で、連絡および調整を行っていなかったこと。
- 屋内作業場の範囲が狭いため、特に雨天は、フォークリフトと労働者の距離が近づき、接近による危険性が高くなっていたこと。
労災要因を見ると、「作業半径に人を入れてしまった」と言う点が大きな要因です。
フォークリフト安全5原則で言うと、
「進行方向への指差し呼称」や「作業半径に人を入れない」を守っていれば労災事故は防げたかも知れません。
激突され
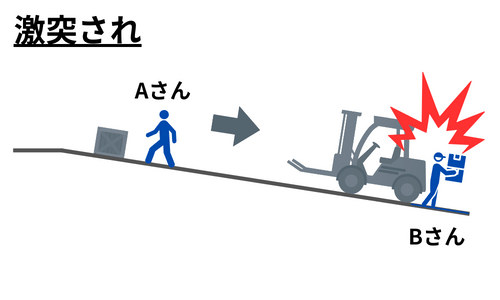
本災害は、ビル新築工事において、地上と地下駐車場を結ぶ通路の途中に駐車させたフォークリフトが逸走し、その通路で別の作業を行っていた作業者に激突したものである。
Aは荷物を移動後、エンジンは切ったものの、サイドブレーキを引かなかった。そのため、しばらくすると、フォークリフトは逸走し始め、Bをはねた。フォークリフトを駐車させた位置は勾配4度の斜面であった。
- 勾配4度の斜面にフォークリフトを駐車させたこと。
- フォークリフト運転者が、運転席を下りたとき、サイドブレーキを引かなかったこと。
- フォークリフトの運転に係る作業が行われているのと同時に、他の事業場が行う作業が行われていたこと。
労災要因を見ると「フォークリフトの基本作業ができていない」ことが要因として大きいです。
サイドブレーキを引くと言う基本的な動作ですが、
普段から指差し呼称確認や車輪止めの使用を行っていれば防げたはずです。
フォークリフト安全5原則で言うと、
「作業半径に人を入れない」という点を守っていれば労災事故は防げていたかも知れません。
墜落・転落
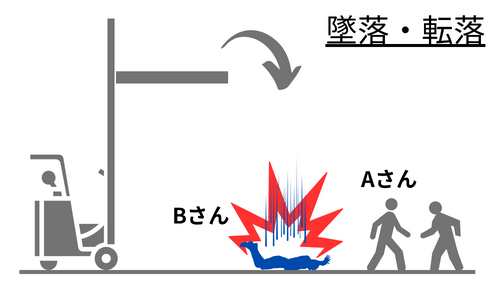
この災害は、コンクリート製品製造工場建屋の入口にひさしを取り付ける工事の準備作業中に発生したものである。
建屋入口の上部(高さ5m)には鳩よけ用のネットが張ってあり、作業を行うためには、それを取り外す必要があった。
そこで、Aは、借りてきたフォークリフトのフォークを5段積みしたパレットに差し込み、そのパレット上にBを乗せて、鳩よけ用のネットの取り外しができる高さ(地上から約4.5m)にまで上昇させた後、フォークリフトのエンジンを止め、Bに作業させた。
作業中にBはパレットから転落し、病院に搬送されたが死亡した。
- 作業計画を作成せずに作業を開始したこと。
- 墜落防止のための措置を講じた安全な作業床を設けなかったこと。
- 安全衛生教育を実施していなかったこと。
労災要因を見ると「フォークリフトの用途外使用を行っている」ことが要因として大きいです。
先程も触れましたが死亡率が最も高いのは「墜落・転落」です。
基本的にフォークリフトの用途外使用をしてはいけません。
パワーもあり高所に簡単に荷物を運べるフォークリフトですが、
荷物だけ運搬可能なので用途外で乗ることは絶対にやめて下さい。
転倒事故

この災害は、フォークリフトを運転して移動中に発生したものである。
AはBにフォークリフトを取りに行くよう指示し、本社事務所でキーが挿入されたままのフォークリフトを運転して建物の角で右折したところ、フォークリフトがスリップし、転倒した。Bは運転席から投げ出され、転倒したフォークリフトのヘッドガードの下敷きとなった。Bは病院に搬送されたが、死亡した。
Bは、フォークリフト運転技能講習を修了しておらず、AもBがフォークリフト運転の資格を持っていないことを知っていた。
また、転倒したフォークリフトは、毎朝の作業前にエンジンオイルと冷却水を点検していたが、タイヤはすり減っていて溝がなかった。さらに、月例検査、年次検査(特定自主検査)は実施されていなかった。
- フォークリフトの運転を無資格者に指示したこと。
- フォークリフトの点検や整備が適切に実施されていなかったこと。
- フォークリフトにキーが挿入されたまま誰でも使える状態で置いていたこと。
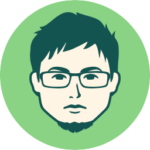
これは全てにおいて最悪の労災事例です。
呆れ果ててしまいますね……。
労災要因を見ると、「無資格者に運転させてしまった」という点が大きな要因です。
この労災事例でもあるように
フォークリフトの点検を怠っていると、重大な事故に繋がります。
フォークリフトの使用条件や走行する環境によっては転倒のリスクが跳ね上がります。
タイヤ以外にも天候や路面にも十分に注意しましょう。
フォークリフト安全5原則で言うと、
「10km/以上出さない」や「急旋回をしない」という点を守るべきでした。
飛来・落下
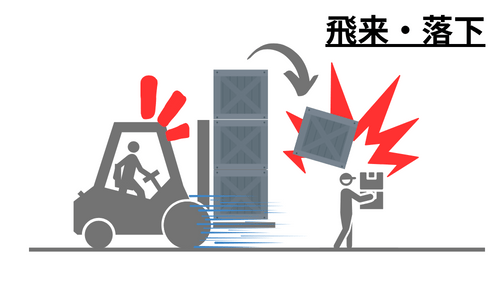
フォークリフトにより積載し、後進して、その後前進させたところ、梱包のため不良品の素材を片付けていたパート作業者を前方に発見し、フォークリフト運転者が急ブレーキをかけた瞬間、フォークに積載していた最上段のパレットが前方へ落下し、パート作業者に激突した。
- 4段積みパレットの重量は下段から95kg、130kg、30kg、130kgと重心が高く、しかもフォークの根元までパレットが入っていない不安定な状態であったこと。
- フォークリフト作業範囲へほかの作業者が立ち入ったこと。
- 前方に、ほかの作業者を発見したため急ブレーキをかけたこと。
- フォークリフトとの接触防止のための誘導者を配置しなかったこと。
労災要因を見ると、「不安定な荷物を乗せた状態で前方確認不足」や「作業エリアの共有」をしてしまっていたのが大きな要因です。
この場合、誘導員がいれば指示に従って安全に作業を行えていたかも知れません。
フォークリフト安全5原則で言うと、
「10km/以上出さない」「進行方向への指差し呼称」「作業半径に人をいれない」という点を守るべきでした。
安全な運転方法と労災事故の対策
フォークリフトの安全な運転方法や労災事故を予防するための対策について詳しく解説します。
労災事故の予防に必要な基本ルールを学び、正しく理解することで、
作業時の危険行為を防ぎます。
労災事故を防ぐための補足と、フォークリフトの基本ルールや停車ルールについても紹介します。
フォークリフトの安全運転について
フォークリフトを安全に運転するにははルールや基本事項の遵守が欠かせません。
安全のためのルールや基本事項について学びましょう。
フォークリフト安全5原則
最初で紹介した通りです。
フォークリフト運転時はこのルールを遵守しましょう。
補足ルール
フォークリフト安全5原則に加えて補足ルールも紹介します。
工場内で作業していて特に注意したらいいと思った点をまとめました。
これらも合わせてルール化しましょう。
僕の工場では死角が多いので特に気をつけています。
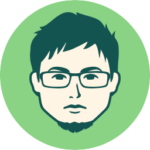
急いでいると走って移動することもあるよね。
もし、死角から人が飛び出してきたら……。
労災事故の予防に必要なフォークリフトのルール
フォークリフトの基本的なルールと停車時のルールについて紹介します。
基本的というだけあって当たり前と感じるかも知れませんが、意外とバカにできません。
労災事故でもあったように停車ルールもしっかり守りましょう。
フォークリフトの基本ルール
- キーの挿しっぱなし禁止
- 運転中の通話禁止
- 指差し呼称による周囲確認
- 誘導員の指示に従う
- フォークリフトの用途外使用禁止
- 作業エリアの遵守
フォークリフト基本ルールを遵守して、作業現場をより良くしましょう。
この中でも、特に用途外使用に関しては労災事故に直結する可能性があるので絶対にしないように注意しましょう。
フォークリフト停車ルール
走行時も大切ですが、停車の際もしっかりルールを守りましょう。
車輪止めをしていなかった為、物損事故や労災事故になった例はいくつもあります。
- サイドブレーキをかける
- フォークを最降下位置に降ろす
- 平地の決められた場所に駐車する
- 前進レバーを中立にする
- 車輪止めをかける
労災事例でもあったように停車した際のサイドブレーキのかけ忘れがありました。
確実にサイドブレーキを掛けるのは勿論、車輪止めもしっかりしましょう。
停車位置を決めておくことでフォークリフトの位置が定まり、作業環境が良くなります。
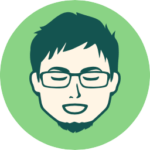
もしサイドブレーキを忘れても車輪止めがあるので安心です。
作業前KY(危険予知)の実施
自分の作業に取り掛かる前に作業前危険予知を行うことがおすすめです。
事前に「危険な環境や行動」を作業者間で洗い出して、指差し呼称のテーマを決めるので作業中の安全意識が向上ができます。
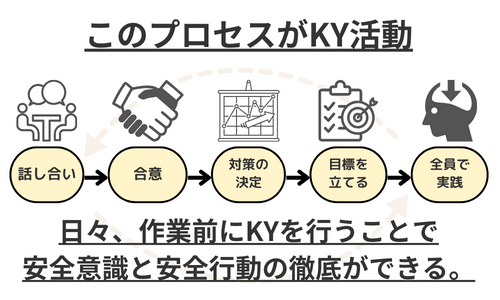
労災事故は
危険な環境と危険な行動が重なった時に
起きると言われています。
日々、作業者間で様々な意見を出し合うことで、
多くの「危険な状態や行動」をインプットできます。
その結果、作業時に自然と危険予知ができるようになり、労災事故の防止に繋がります。
また、指差し呼称は目視と動作と発声をすることで確認をしっかり行えます。
職種を選ばず、確認作業全般で活かせるので取り入れましょう。
指差し呼称の手順
- 対象をしっかり目視する。
- 声に出しながら対象を指でさす。
- さした指を耳元へ戻す。
- 右手の指でさしたら、右の耳元まで戻しながら、確認事項が本当に正しいか、本当に合っているかを心の中で反すうし、再確認します。
- 「ヨシっ!」と発声しながら右手を振り下ろす。
ある実験データでは、
「何もしなかったときと比べ、ミスを1/6に減少させるという結果が確認されている」
ということです。
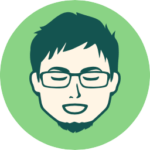
鉄道会社で取り入れられているのも納得ですね。
まとめ
今回はフォークリフト安全5原則について紹介しましたが、
安全な運転方法や労災事故の対策のポイントもおさらいしていきましょう。
- フォークリフト安全5原則+3つの補足ポイント
- フォークリフトの基本ルール
- フォークリフトの停車ルール
- KY活動の実施
以上のようにフォークリフトの安全5原則だけではなく、
基本的なルールや停車ルールを守ることでより安全な環境を整えていくことが可能です。
また、最後でも触れましたが、
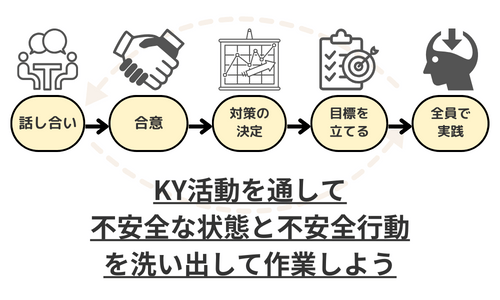
ヒューマンエラーは必ず起きるので、
事前に危険箇所や危険行動の話し合いをする事で、
作業者間での自然な情報交換となります。
その結果、作業場全体での安全意識の向上と安全行動の徹底ができるようになります。
職種を選ばず、指差し呼称の実践をして確認をしっかりと行いましょう。
長くなりましたが、ここまで読んで頂いた方、本当にお疲れ様です。
この記事が誰かの役に立ってくれると嬉しいです。
それでは、今日もご安全に!
コメント